Additive Fertigungstechnologien im Vergleich
3D-Metalldruck

Sind Sie bereit, Ihre Teile per DMLS 3d-drucken zu lassen?
Sofortangebot erhalten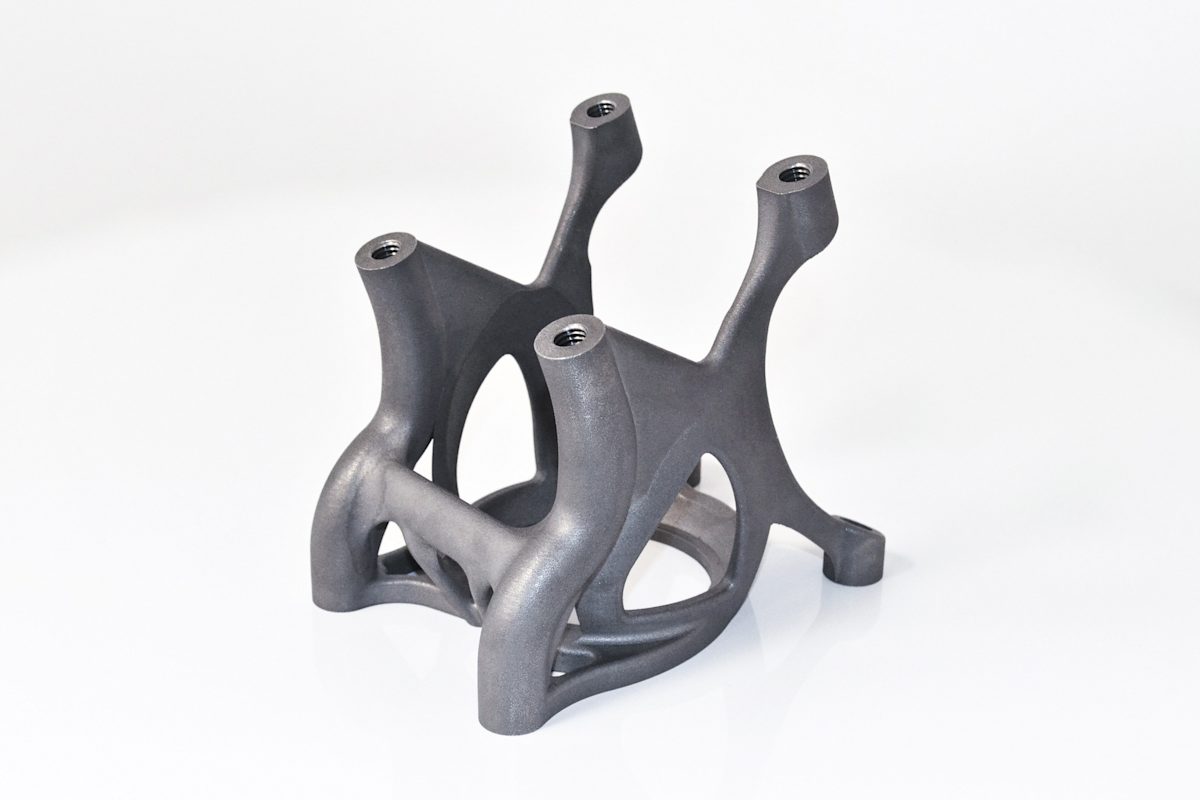
Der Metall-3D-Druck wird immer beliebter. Dieser Leitfaden zeigt Ihnen, wie Sie das Meiste aus der additiven Fertigung mit Metall herausholen. Sie erhalten einen umfassenden Überblick über die Metall-3D-Druck-Landschaft von heute und erfahren mehr über die einzigartigen Vorteile und Einschränkungen dieses Verfahrens sowie wann und wie Sie die drei beliebtesten Metall-3D-Druckverfahren nutzen: DMLS/SLM, Binder-Jetting und Materialextrusion. Falls Sie mithilfe des Metall-3D-Drucks gefertigte Teile benötigen, sehen Sie sich bitte die Metall-3D-Druckdienste von Protolabs an.
Part 1
3D Druck Metall: Die Grundlagen
Wie funktionieren 3D-Metalldrucker? Was sind ihre wichtigsten Vorteile und Einschränkungen? Wie wird der 3D-Metalldruck heute in der Industrie eingesetzt?
In diesem Abschnitt werden wir diese Fragen beantworten und mehr über die grundlegenden Mechanismen jedes 3D-Metalldruckprozesses erfahren. Durch den Vergleich mit der „traditionellen“ Fertigung erhalten Sie ein tieferes Verständnis für den aktuellen Stand des 3D-Metalldrucks und dessen großes Potenzial.
Wie funktionieren 3D-Metalldrucker?
Ähnlich wie bei allen anderen 3D-Druckverfahren verarbeiten 3D-Metalldrucker Teile, indem sie auf der Grundlage eines digitalen 3D-Designs jeweils eine Materialschicht hinzufügen - daher der alternative Begriff „Additive Fertigung“.
Auf diese Weise können Teile mit Geometrien hergestellt werden, die keine „herkömmliche“ subtraktiver (CNC-Bearbeitung) oder formgebenden (Metallguss-)Technologien erfordern, also ohne spezielle Werkzeuge (z. B. eine Form).
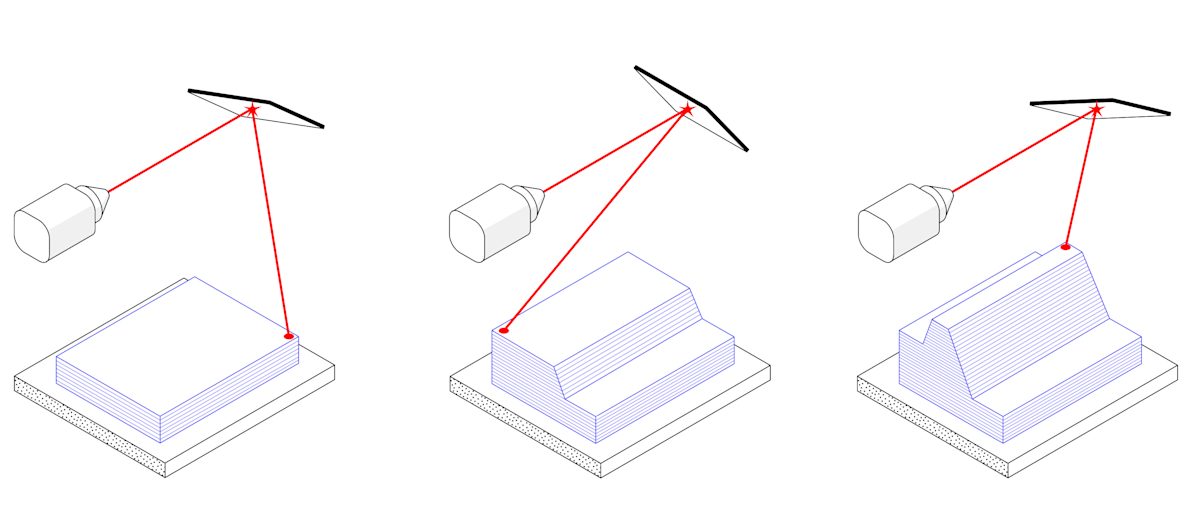
Ab hier variieren die spezifischen Schritte, die jeder 3D-Metalldrucker zur Herstellung eines Teils durchführt, je nach Technologie erheblich:
Pulverbettfusion
Ein Hochleistungslaser (beim DMLS/SLM) oder ein Elektronenstrahl (beim EBM) wird verwendet, um Metallpulverpartikel selektiv miteinander zu verschmelzen, wobei Schicht für Schicht das Metallteil gebildet wird.
Hersteller: EOS, 3D Systems, Renishaw, SLM Solutions, Concept Laser, Arcam
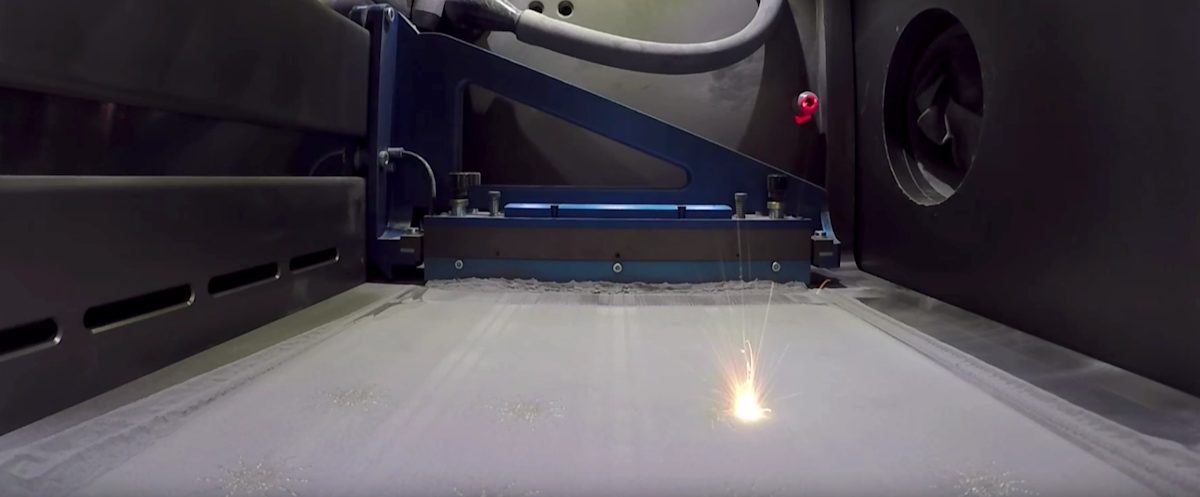
Binder Jetting
Metallpulverteilchen werden Schicht für Schicht mit einem Klebstoff zusammengebunden und bilden ein „rohes“ Teil, das thermisch nachbearbeitet (gesintert) werden muss, um das Bindemittel zu entfernen und ein vollständig metallisches Teil zu erhalten.
Hersteller: Desktop Metal, ExOne, Digital Metal, HP
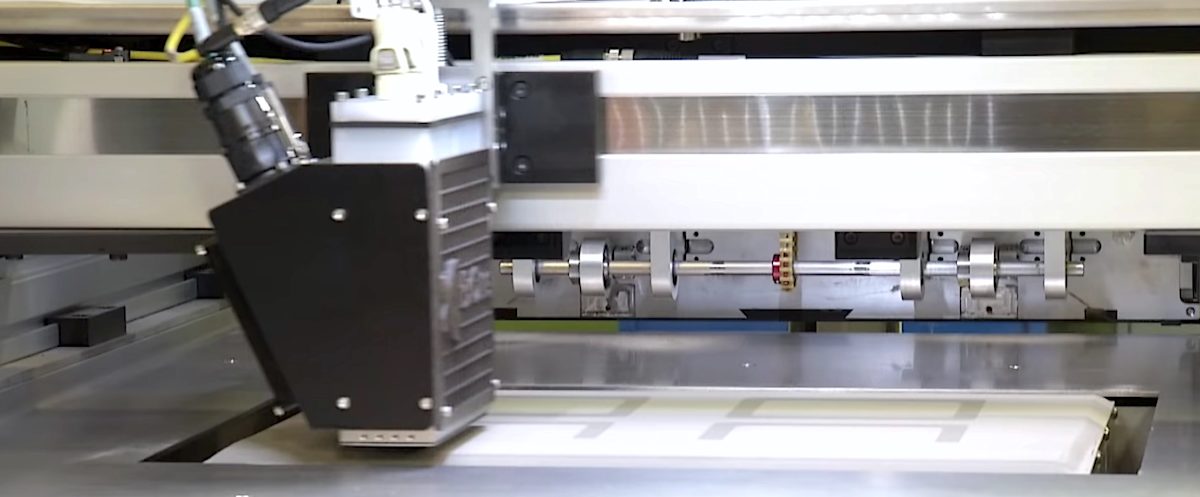
Extrusion von Metallwerkstoffen
Ein aus Polymer bestehender, stark mit Metallpulver vermischter Faden oder Stab wird durch eine Düse extrudiert (wie beim FDM), um den Rohling zu formen, der dann nachbearbeitet (von Binder befreit und gesintert) wird, um ein Vollmetallteil zu erhalten.
Hersteller: Desktop Metal, Markforged
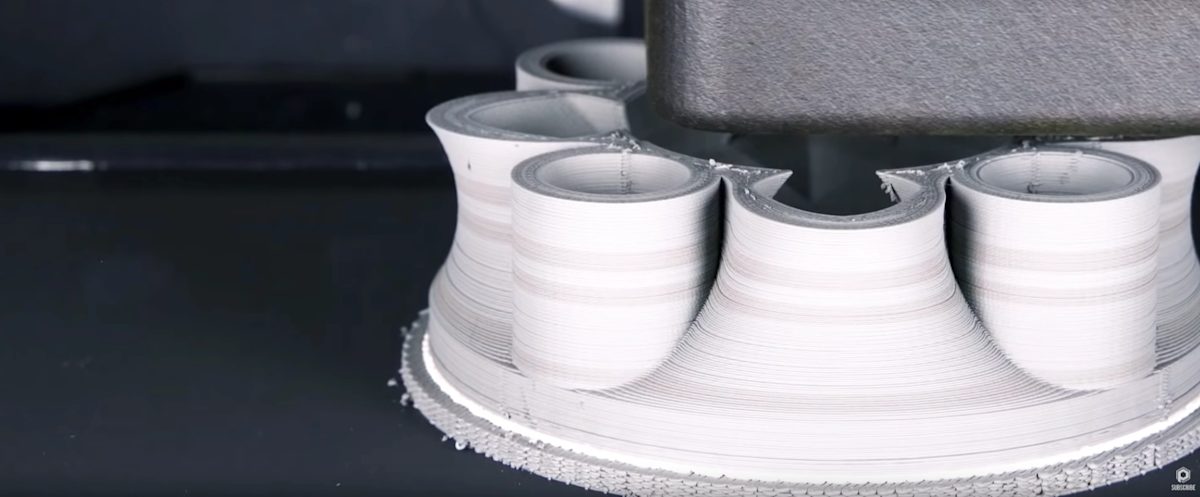
Additive Fertigung mit Ultraschall
Metallfolien werden durch Ultraschallschweißen Schicht für Schicht verbunden und anschließend durch CNC-Bearbeitung in die gewünschte Form gebracht.
Hersteller: Fabrisonic
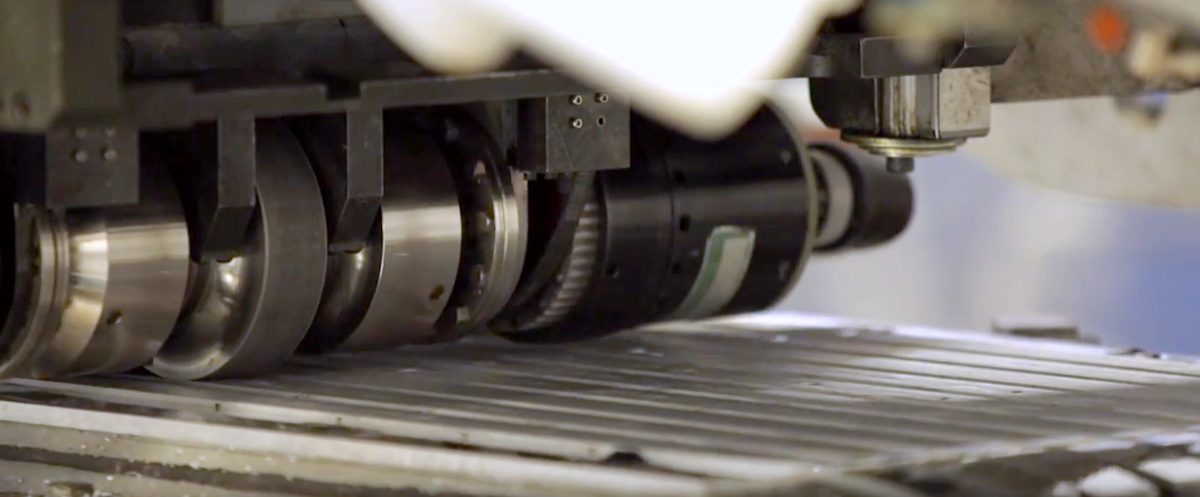
Weitere Prozesse
Im Laufe der Jahre wurden andere 3D-Metalldrucksysteme entwickelt, die auf etablierten Kunststoff-3D-Drucktechnologien (wie Materialauftrag per Düse oder SLA) basieren.
Der 3D-Druck wird mittlerweile auch zur Erstellung von Werkzeugen für die „traditionelle“ Metallherstellung verwendet, z. B. Sandguss oder Feinguss.
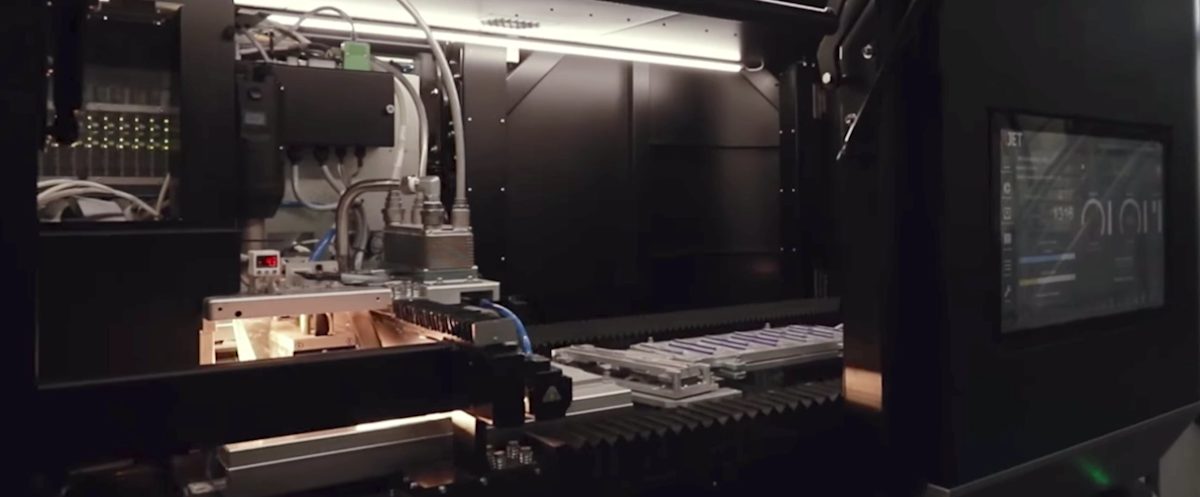
Die heute am häufigsten verwendeten 3D-Metalldruckverfahren sind Direct Metal Laser Sintering (DMLS) / Selective Laser Melting (SLM), gefolgt von Binder Jetting und Metallextrusion.
Wenn Sie sich eingehender mit den grundlegenden Mechanismen, den besonderen Vorteilen und Einschränkungen sowie den Funktionen jeder dieser Technologien befassen möchten, fahren Sie direkt mit dem nächsten Teil dieses Handbuchs fort.
Im weiteren Verlauf dieses Abschnitts konzentrieren wir uns auf die allgemeinen Aspekte des 3D-Metalldrucks, die für alle Prozesse gelten. Wir werden auch untersuchen, wie sie sich mit „traditionellen“ Herstellungsprozessen vergleichen lassen. Auf diese Weise erhalten Sie ein umfassenderes Verständnis dafür, wie Sie diese einzigartige Fertigungstechnologie optimal nutzen können. Aber zuerst eine kurze Geschichtsstunde…
Eine kurze Geschichte des 3D-Metalldrucks
- Ende der 80er Jahre entwickelte Dr. Carl Deckard von der University of Texas den ersten Laser-Sinter-3D-Drucker für Kunststoff. Diese Erfindung ebnete den Weg für den 3D-Metalldruck.
- Das erste Patent zum Laserschmelzen von Metallen wurde 1995 vom Fraunhofer-Institut in Deutschland eingereicht. Firmen wie EOS und viele Universitäten führen die Entwicklung dieses Prozesses an.
- 1991 stellte Dr. Ely Sachs vom MIT ein 3D-Druckverfahren vor, das heute besser unter dem Namen Binder Jetting bekannt ist. Der Binderauftrag für Metall wurde 1995 an ExOne lizenziert.
- Der 3D-Metalldruck verzeichnete in den 00er Jahren ein langsames, aber stetiges Wachstum. Dies änderte sich nach 2012, als die ursprünglichen Patente abliefen und große Investitionen von Unternehmen wie GE oder [HP](https:// www8.hp.com/us/en/printers/3d-printers.htm) und DM getätigt wurden.
- Heute schätzt der Wohler-Bericht, dass der 3D-Metalldruck ein 720-Millionen-Dollar-Markt ist und schnell wächst. Alleine im Jahr 2017 stieg der Umsatz mit 3D-Metalldruckern um 80%.

Vorteile und Einschränkungen des 3D-Metalldrucks
Es ist wichtig zu verstehen, dass der 3D-Metalldruck ein leistungsstarkes Werkzeug ist, das viele einzigartige Vorteile bietet. Aufgrund seiner derzeitigen Beschränkungen ist er jedoch nicht immer die beste Wahl, wenn es um die Herstellung von Metallteilen geht.
Hier haben wir die wichtigsten Vor- und Nachteile des 3D-Metalldrucks zusammengefasst. Nutzen Sie sie, um zu verstehen, wo der 3D-Metalldruck heute steht und wohin er in naher Zukunft führen wird.
Vorteile des 3D-Metalldrucks
Der größte Vorteil des 3D-Metalldrucks im Vergleich zur „traditionellen“ Fertigung liegt in seiner außergewöhnlichen Gestaltungsflexibilität. Da kein spezielles Werkzeug erforderlich ist (z. B. eine Form oder ein Schneidwerkzeug), können Geometrien, die mit anderen Verfahren nicht hergestellt werden können, problemlos in 3D gedruckt werden.
Noch wichtiger ist, dass die Erhöhung der geometrischen Komplexität eines Teils fast keine Auswirkungen auf die Herstellungskosten hat. Dies bedeutet, dass beim 3D-Metalldruck topologieoptimierte organische Strukturen verwendet werden können, um die Leistung der produzierten Teile erheblich zu verbessern.
Erfahren Sie, wie Sie Entwürfen für den 3D-Metalldruck erstellen →
Die große Designflexibilität des 3D-Metalldrucks geht Hand in Hand mit der Schaffung von Leichtbaustrukturen. Die Befolgung der besten Entwurfspraktiken für den 3D-Metalldruck bietet immer eine leichtgewichtige Lösung.
Zu diesem Zweck werden in der Regel fortgeschrittene CAD-Techniken wie Topologieoptimierung und generatives Design verwendet.
Dies führt zu Teilen mit sowohl geringerem Gewicht (typischerweise um 25% bis 50%) als auch höherer Steifheit. Dies ist der Schlüssel für High-End-Anwendungen in Branchen wie der Luft- und Raumfahrt.
Erfahren Sie, wie Sie Entwürfen für den 3D-Metalldruck erstellen →
Da die Werkzeugzugänglichkeit beim 3D-Metalldruck kein Thema ist, können auch Teile mit Innenstrukturen hergestellt werden.
Beispielsweise sind interne Kanäle für die gleichmäßige Kühlung eine hervorragende Möglichkeit, die Leistung eines Teils zu steigern. Spritzgusskerne mit gleichmäßiger Kühlung - hergestellt mit DMLS/SLM - können die Einspritzzyklen um bis zu 70% verkürzen.
Ein weiteres Beispiel für eine verbesserte Teilefunktionalität ist die Metallextrusion. Mit diesem Verfahren können bei Bedarf kundenspezifische Vorrichtungen und Einspannungen mit komplexen Geometrien erstellt werden, um die Effizienz der Abläufe anderer industrieller Prozesse in der Produktion zu steigern.
Eine weitere Stärke des 3D-Metalldrucks ist die Möglichkeit, eine Baugruppe zu einem einzigen Teil zusammenzuführen.
Dadurch sind keine Befestigungselemente mehr erforderlich, und es entstehen Teile, die mehrere Funktionen gleichzeitig erfüllen können. Außerdem werden Arbeitskosten und Vorlaufzeiten minimiert und die Wartungs- und Serviceanforderungen verringert.
Als zusätzlicher Vorteil ist die Reduzierung der Gesamtteilezahl eine weitere Methode zur Erstellung von Leichtbaustrukturen.
Selbst wenn ein Teil mit komplexer Geometrie mit „traditionellen“ Methoden hergestellt werden kann, können dazu 20 oder mehr Produktionsschritte erforderlich sein.
In diesen Fällen sollte der 3D-Metalldruck als echte Fertigungsoption angesehen werden. Mit Binder Jetting kann beispielsweise die Gesamtanzahl der Bearbeitungsschritte auf fünf oder weniger reduziert werden (einschließlich Nachbearbeitung und Endbearbeitung). Auf diese Weise wird die Komplexität der Fertigungslieferkette erheblich reduziert.
Im Gegensatz zum 3D-Druck von Kunststoffen weisen mit DMLS/SLM oder Binder Jetting hergestellte Teile ein isotropes mechanisches Verhalten auf. Auch ihre Materialfestigkeit ist vergleichbar mit Schmiedemetall (und in einigen Fällen sogar besser). Aus diesem Grund finden mittlerweile 3D-gedruckte Metallteile in den anspruchsvollsten Branchen wie der Luft- und Raumfahrt ihre Anwendung.
Beachten Sie jedoch, dass 3D-Druckteile im Allgemeinen eine geringere Dauerfestigkeit aufweisen. Dies ist auf ihre Oberflächenrauheit und ihre innere Porosität zurückzuführen (typischerweise haben DMLS-/SLM-Teile eine Porosität von <0,2% und Binder Jetting-Teile von <2%).
Einschränkungen des 3D-Metalldrucks
Im Vergleich zu herkömmlichen Herstellungsverfahren sind die Kosten für den 3D-Metalldruck heutzutage beträchtlich. Durchschnittlich kostet ein typisches DMLS/SLM-Teil ca. 5.000 bis 10.000 US-Dollar für den 3D-Druck und die Oberflächenbearbeitung. Daher ist zu beachten, dass der Einsatz von 3D-Metalldruck nur dann wirtschaftlich sinnvoll ist, wenn er mit einer erheblichen Leistungsverbesserung verbunden ist.
Es besteht jedoch ein Bedarf an erschwinglichen 3D-Metalldrucklösungen. Die neuen „Benchtop“-Metallextrusionssysteme und Binderauftrag-Strahlsysteme für die Produktion könnten diese Lücke in naher Zukunft schließen.
Eine weitere Einschränkung des 3D-Metalldrucks besteht darin, dass er bei größeren Auflagen noch nicht mit der herkömmlichen Fertigung mithalten kann.
Das Fehlen von Spezialwerkzeugen führt zu geringen Anlaufkosten, aber auch dazu, dass die gesamten Herstellungsstückkosten nicht wesentlich vom Produktionsvolumen beeinflusst werden. Mit anderen Worten, der Stückpreis bleibt bei höheren Stückzahlen nahezu unverändert, und es können keine Skaleneffekte eingesetzt werden.
Die Branche arbeitet jedoch an 3D-Metalldrucksystemen, mit denen die Produktion rationalisiert werden kann. So kommen derzeit beispielsweise DMLS/SLM-Maschinen mit mehreren Lasern und Binderauftrag-Systemen auf den Markt, die eine kontinuierliche Produktion ermöglichen.
Das Entwerfen von Teilen für den 3D-Metalldruck folgt anderen Regeln als für die „traditionelle“ Fertigung. Dies führt häufig dazu, dass bestehende Entwürfe neu gestaltet werden müssen.
Darüber hinaus sind die Tools älterer CAD-Software möglicherweise nicht ausreichend, um die Vorteile des 3D-Metalldrucks voll auszuschöpfen. Um eine umfassende Einführung in die wichtigsten Konstruktionsaspekte, erweiterte CAD-Tools und Konstruktionsregeln für den 3D-Metalldruck zu erhalten, springen Sie zum letzten Abschnitt dieses Handbuchs.
Nahezu jedes 3D-gedruckte Metallteil muss nachbearbeitet werden, bevor es einsatzbereit ist. Dies erhöht die Gesamtkosten und die Fertigungszeit.
Unabhängig von der gewählten Technologie sind für die Herstellung des endgültigen Teils fast immer Kombinationen aus Wärmebehandlung, Bearbeitung, Polieren und anderen Endbearbeitungsverfahren erforderlich. Weitere Informationen zu den erforderlichen Nachbearbeitungsschritten für jede Technologie finden Sie in späteren Abschnitten.
Anwendungen des 3D-Metalldrucks
Hier haben wir Beispiele für wichtige industrielle Anwendungen des -3D- Metalldrucks zusammengestellt. Sie veranschaulichen einige der Hauptvorteile und -einschränkungen der Technologie. Nutzen Sie die Beispiele, um einen Einblick zu bekommen, warum Ingenieure -3D- Metalldruck jeweils für ihre spezielle Anwendung gewählt haben.
Materialien für den 3D-Metalldruck
Die Anzahl der für den 3D-Metalldruck verfügbaren Metallmaterialien nimmt rapide zu. Ingenieure können heute aus folgenden Legierungen auswählen:
- Edelstähle
- Werkzeugstähle
- Titanlegierungen
- Aluminiumlegierungen
- Superlegierungen auf Nickelbasis
- Kobalt-Chrom-Legierungen
- Legierungen auf Kupferbasis
- Edelmetalle (Gold, Silber, Platin …)
- Exotische Metalle (Palladium, Tantal …)
Die Kosten für den 3D-Metalldruck
Die Kosten für einen 3D-Metalldrucker variieren stark zwischen den Technologien. Der Verkaufspreis eines DMLS-/SLM-Druckers liegt im Durchschnitt bei 550.000 USD und kann 2 Millionen USD erreichen. Metallbinder-Strahlsysteme kosten ungefähr 400.000 US-Dollar. Ein Metall-Extrusionsdrucker kostet Sie einschließlich der Nachbearbeitungseinheiten etwa 140.000 US-Dollar.
Die Herstellungskosten eines typischen DMLS-/SLM-Teils betragen ca. 5.000 bis 10.000 USD (einschließlich Endbearbeitung). Bei Binderauftrag mit Düse und Metallextrusion können die Kosten pro Teil bis zu 5-10 mal niedriger sein als bei DMLS-/SLM-Teilen. Zum jetzigen Zeitpunkt ist es jedoch noch zu früh, die vollen Betriebskosten dieser Systeme zu ermitteln.
Die folgende Tabelle enthält eine Aufschlüsselung der durchschnittlichen Kosten der verschiedenen Herstellungsschritte für DMLS/SLM. Beachten Sie, dass die Materialkosten sowie die Kosten für die Nachbearbeitung erheblich zu den Gesamtkosten beitragen.
Produktionsschritt | Bedienung | Kosten |
---|---|---|
Herstellung | Materialkosten | 200 USD - 500 USD pro Kilogramm |
DMLS-/SLM-Kosten | $ 2.000 - $ 4.000 pro Rohling † | |
Nachbearbeitung | Spannungsabbau | $ 500 - $ 600 pro Rohling † |
Entfernung des Teils/der Stützen | $ 100 - $ 200 pro Teil | |
Wärmebehandlung / HIP | $ 500 - $ 2.000 pro Rohling † | |
CNC-Bearbeitung | $ 500 - $ 2.000 pro Teil | |
Oberflächenbehandlungen | $ 200 - $ 500 pro Teil |
† In der Regel passen sechs bis zwölf Teile auf dieselbe Rohlingplatte.
Die Geschwindigkeit des 3D-Metalldrucks
Unabhängig vom Prozess benötigt ein 3D-Metalldruckteil mindestens 48 Stunden und durchschnittlich 5 Tage , um hergestellt und fertigbearbeitet zu werden.
Etwa 50% der gesamten Produktionszeit entfallen auf den Druck. Dies hängt natürlich vom Teilevolumen und dem Bedarf an Stützstrukturen ab. Als Referenz variiert die aktuelle Produktionsgeschwindigkeit moderner 3D-Metalldrucksysteme zwischen 10 und 40 cm³/h.
Die verbleibende Produktionszeit hängt mit den Nachbearbeitungs- und Veredelungsanforderungen zusammen. Wärmebehandlungen tragen erheblich zur Gesamtproduktionszeit bei: Ein typischer Wärmezyklus dauert 10 bis 12 Stunden. Mechanische Oberflächennachbehandlungen können auch ein zeitaufwändiger Schritt sein, da sie von einem Experten (5-Achsen-CNC-Bearbeitung) oder von Hand (Handpolieren) durchgeführt werden müssen.
3D-Metalldruck vs. traditionelle Fertigung
Beginnen Sie immer mit einer Kosten-Leistungs-Analyse , wenn Sie zwischen einem 3D-Metalldruck und einer subtraktiven (CNC-Bearbeitung) oder formgebenden (Metallguss-)Technologie wählen.
Generell hängen die Herstellungskosten hauptsächlich vom Produktionsvolumen ab, während die Leistung eines Teils stark von seiner Geometrie abhängt.
Die Stärke des 3D-Metalldrucks liegt in der Fähigkeit, Teile mit komplexen und optimierten Geometrien zu erstellen. Dies macht ihn ideal für die Herstellung von Hochleistungsteilen. Andererseits skaliert er nicht so gut wie CNC-Bearbeitung oder Metallguss bei höheren Stückzahlen.

Als Faustregel gilt:
Die hohen Kosten des 3D-Metalldrucks sind nur dann finanziell zu rechtfertigen, wenn sie mit einer signifikanten Steigerung der Leistung oder der betrieblichen Effizienz verbunden sind.
Selbstverständlich erfüllt jedes 3D-Metalldruckverfahren unterschiedliche industrielle Anforderungen. Verwenden Sie die folgenden Tipps als allgemeine Richtlinien, um zu verstehen, welcher Prozess für Sie am besten geeignet ist:
- DMLS/SLM ist die beste Lösung für Teile mit hoher geometrischer Komplexität (organische, topologieoptimierte Strukturen), die hervorragende Materialeigenschaften erfordern, um die Effizienz der anspruchsvollsten Anwendungen zu steigern.
- Binder Jetting ist die beste Lösung für die Produktion in kleinen bis mittleren Serien, welche die hohe wirtschaftliche Investition eines Formgebungsverfahrens nicht rechtfertigen, sowie für Teile mit Geometrien, die mit einem subtraktiven Verfahren nicht effizient hergestellt werden können.
- Metallextrusion ist die beste Lösung für Metallprototypen und Einzelteile mit Geometrien, die ansonsten für die Fertigung eine [5-Achsen-CNC-Maschine] (https://www.hubs.com/de/leitfaden/zerspanung/#5-axis-cnc-machining) erfordern würden.
Die folgende Tabelle ist eine Matrix aus : Volumen vs. Teilekomplexität , welche die Bereiche zeigt, in denen jeder Herstellungsprozess (additiv, subtraktiv oder formgebend) seine beste Leistung erbringt. Verwenden Sie diese als Referenz:
Menge | Geringe Komplexität | Titel | Titel |
---|---|---|---|
< 10 Teile | CNC-Bearbeitung | Metallextrusion CNC-Bearbeitung |
DMLS/SLM |
< 100 Teile | CNC-Bearbeitung | Binder Jetting CNC-Bearbeitung |
Binder Jetting DMLS/SLM |
< 1000 Teile | CNC-Bearbeitung Metallguss |
Binder Jetting CNC-Bearbeitung |
Binder Jetting |
> 1000 Teile | Blech Metallguss |
Metallguss | - |
Part 2
DMLS und SLM
Direktes Metall-Lasersintern (DMLS) und selektives Laserschmelzen (SLM) sind die heute am häufigsten verwendeten 3D-Metalldruckverfahren. Sie eignen sich besonders für High-End-Anwendungen, da sie große Gestaltungsfreiheit und fortschrittliche Materialeigenschaften bieten.
In diesem Abschnitt werden wir uns eingehender mit dem Herstellungsprozess, den technischen Eigenschaften sowie den Vorteilen und Einschränkungen dieser beiden sehr ähnlichen Prozesse befassen.
Was ist DMLS-/SLM-3D-Druck?
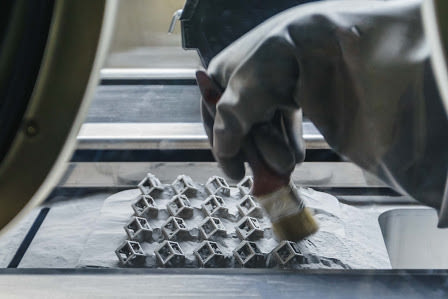
DMLS (Direct Metal Laser Sintering, direktes Metall-Lasersintern) oder SLM (Selective Laser Melting, selektives Metallschmelzen) sind zwei Pulverbettschmelz-3D-Metalldrucktechnologien. Der praktische Unterschied zwischen SLM und DMLS ist sehr gering. Für Designzwecke können die beiden Technologien als gleich behandelt werden.
Beide verwenden einen Hochleistungslaser, um Metallpulverteilchen Schicht für Schicht zu einem Teil zusammenzufügen. SLM erreicht eine vollständige Schmelze, während DMLS die Metallpartikel aufgrund der sehr hohen Temperaturen nur auf molekularer Ebene miteinander verschmelzen lässt. Die meisten Metalllegierungen sind mit dem DMLS-Verfahren kompatibel, während in SLM nur bestimmte (reine) Metallmaterialien verwendet werden können.
Wie funktioniert DMLS/SLM?
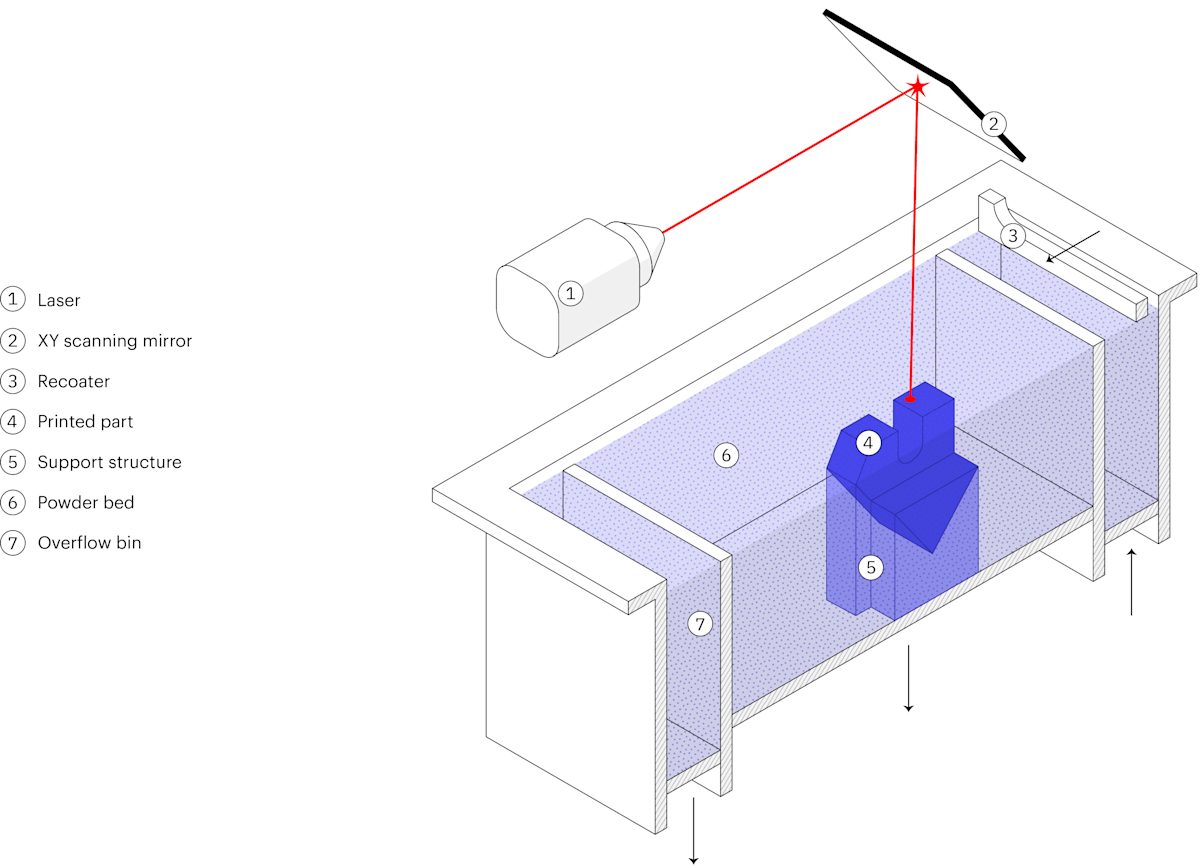
Hier sind die grundlegenden Schritte des DMLS-/SLM-3D-Druckprozesses erklärt:
- Die Rohlingkammer wird zuerst mit Inertgas gefüllt und dann auf die optimale Drucktemperatur vorgeheizt.
- Eine dünne Schicht Metallpulver (typisch 50 μm) wird auf der Rohlingplattform verteilt.
- Der Laser fährt den Querschnitt des Teils ab und bindet die Metallpartikel selektiv.
- Wenn der gesamte Bereich bestrahlt wurde, bewegt sich die Rohlingplattform um eine Schicht nach unten und der Vorgang wird wiederholt, bis der gesamte Rohling fertiggestellt ist.
- Nach dem Drucken muss der Rohling erst abkühlen und dann wird das lose Pulver abgesaugt.
Der 3D-Druckschritt ist erst der Anfang des DMLS-/SLM-Herstellungsprozesses. Nach Abschluss des Druckvorgangs sind mehrere (obligatorische oder optionale) Nachbearbeitungsschritte erforderlich, bevor die Teile einsatzbereit sind. Die obligatorischen Nachbearbeitungsschritte umfassen:
- Entspannung: Durch die sehr hohen Verarbeitungstemperaturen beim Drucken entstehen innere Spannungen. Diese müssen vor jeder anderen Operation durch einen Wärmezyklus freigesetzt werden.
- Entfernung der Teile: Beim DMLS/SLM werden die Teile im Wesentlichen auf die Rohlingplattform geschweißt. Hier wird eine Bandsäge oder ein EDM-Drahtschneider verwendet.
- Entfernung der Stützelemente: Beim DMLS/SLM ist immer eine Abstützung erforderlich, um die beim Drucken auftretenden Verwerfungen und Verzerrungen zu verringern. Die Stützelemente werden manuell entfernt oder per CNC-bearbeitet.
Um die technischen Spezifikationen zu erfüllen, sind häufig zusätzliche Nachbearbeitungsschritte erforderlich. Diese können Folgendes umfassen:
- CNC-Bearbeitung: Wenn engere Toleranzen als der Standard ± 0,1 mm erforderlich sind, wird die Bearbeitung als Endbearbeitungsschritt verwendet. Auf diese Weise wird nur minimal wenig Material entfernt.
- Wärmebehandlungen: Um die Materialeigenschaften des Teils zu verbessern, können Wärmebehandlungen oder heißes isostatisches Pressen (HIP) verwendet werden.
- Glätten / Polieren: Bestimmte Anwendungen erfordern eine glattere Oberfläche als die Standardoberflächenrauheit von-RA 10 μm von DMLS/SLM im gedruckten Zustand. CNC-Bearbeitung und manuelles, Vibro- oder chemisches Polieren sind die verfügbaren Lösungen.
Metallpulver für den 3D-Druck
Der beim DMSL/SLM und vielen anderen 3D-Druckverfahren verwendete Rohstoff liegt in Pulverform vor.
Die Eigenschaften der Metallpulver sind für die Endergebnisse sehr wichtig. Um einen guten Fluss und eine dichte Packung zu gewährleisten, müssen Metallpartikel eine Kugelform und eine Größe zwischen 15 und 45 Mikrometern aufweisen. Um diese hohen Anforderungen zu erfüllen, werden üblicherweise Methoden wie Gas- oder Plasma-Zerstäubung verwendet.
Die hohen Kosten für die Herstellung dieser Metallpulver tragen wesentlich zu den Gesamtkosten des 3D-Metalldrucks bei.
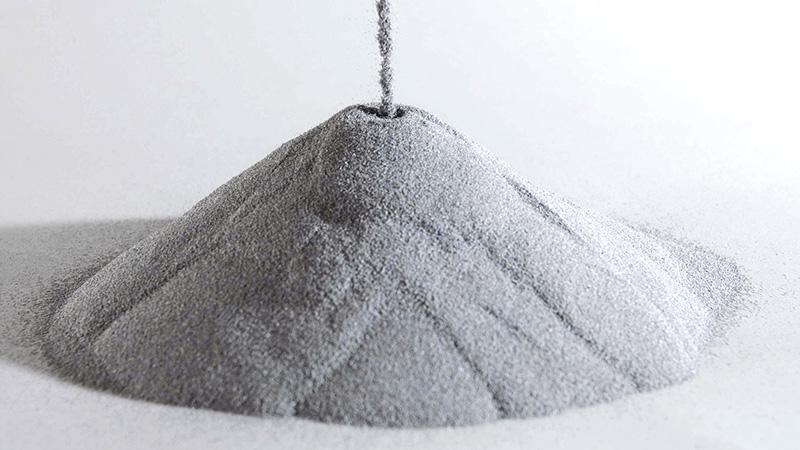
Vorteile und Einschränkungen von DMLS/SLM
Die Hauptstärke von DMLS/SLM ist die Fähigkeit, hochoptimierte organische Strukturen aus Hochleistungsmetalllegierungen zu erzeugen.
Mit DMLS/SLM hergestellte Teile können eine komplexe organische Form haben, die auf geringes Gewicht und gleichzeitig maximale Steifigkeit optimiert ist. Oder sie können interne Geometrien haben, die mit keiner anderen Methode hergestellt werden können.
Die Materialeigenschaften von DMLS-/SLM-Teilen sind hervorragend. Teile fast ohne innere Porosität können aus einer Vielzahl von Metalllegierungen hergestellt werden, von Aluminium und Stahl bis hin zu hochfesten Superlegierungen.
In einem früheren Abschnitt haben wir jedoch festgestellt, dass die mit DMLS/SLM verbundenen Kosten hoch sind. Aus diesem Grund ist es nur wirtschaftlich sinnvoll, diese Verfahren für optimierte Teile in hochwertigen technischen Anwendungen einzusetzen.
Aus technischer Sicht besteht die Haupteinschränkung von DMLS und SLM darin, dass sie umfangreiche Abstützelemente benötigen. Diese werden benötigt, um Verwerfungen zu vermeiden und das Teil auf der Rohlingplattform zu verankern. Frisch vom Drucker ist die Oberflächenrauheit der hergestellten Teile für die meisten technischen Anwendungen relativ hoch, so dass eine Nachbearbeitung erforderlich ist.
Technische Eigenschaften von SLM und DMLS
In der folgenden Tabelle sind die grundlegenden technischen Funktionen eines typischen DMLS-/SLM-3D-Metalldruckers zusammengefasst. Weitere Gestaltungsrichtlinien finden Sie unter Designregeln.
Eigentum | DMLS / SLM |
---|---|
Materialauswahl | Derzeit große Auswahl an Materialien verfügbar Aluminiumlegierungen, Titan, Edelstahl, Werkzeugstahl, Kobalt-Chrom-Legierungen, Nickelsuperlegierungen, Edelmetalle usw. |
Maßhaltigkeit | ± 0,1 mm |
Typische Rohlinggröße | 250 x 150 x 150 mm (bis zu 500 x 280 x 360 mm) |
Gemeinsame Schichtdicke | 20 - 50 μm |
Typische Oberflächenrauheit | RA 8 - 10 μm |
Abstützung | Immer erforderlich |
Innere Porosität | Weniger als 0,2 - 0,5% |
Kosten pro Teil | $$$$$ |
Part 3
Metall Binder Jetting
Der Düsenauftrag von Metallbindemitteln wird immer beliebter. Aufgrund seiner einzigartigen Eigenschaften eignet sich das Verfahren besonders für kleine bis mittlere Auflagen.
In diesem Abschnitt befassen wir uns eingehender mit den Schritten des Binder Jettings und den grundlegenden Eigenschaften der hergestellten Metallteile.
Was ist Metall Binder Jetting?
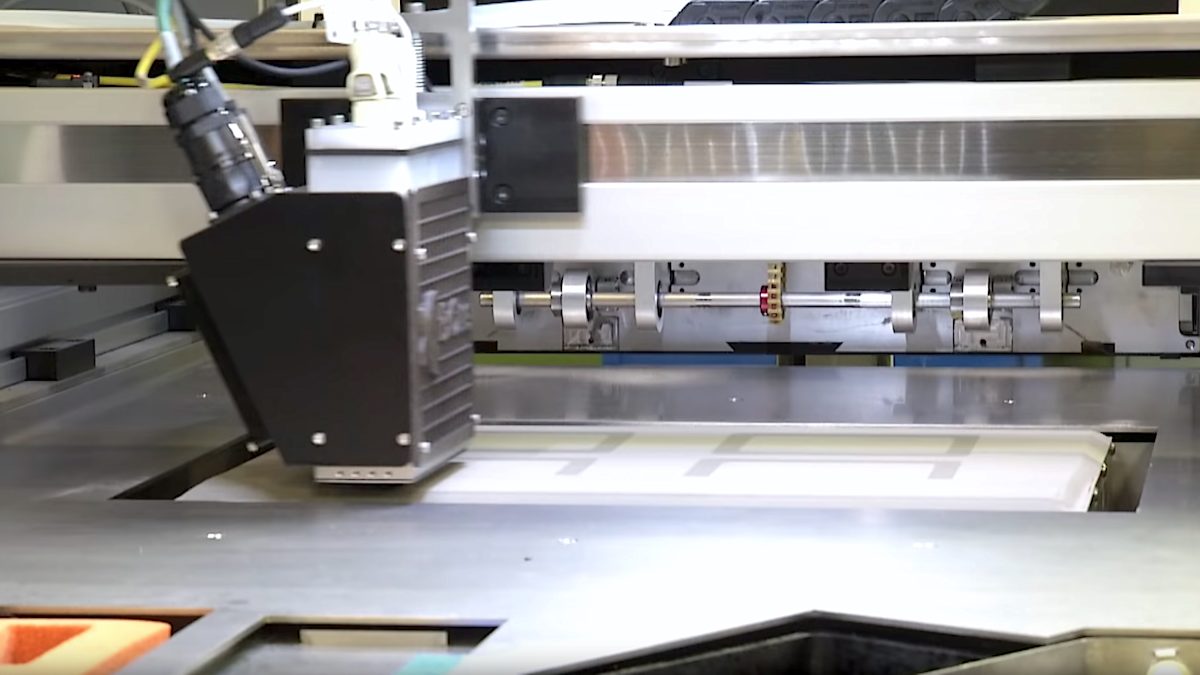
Binder Jetting baut Teile auf, indem ein Bindemittel durch Tintenstrahldüsen auf eine dünne Pulverschicht aufgetragen wird. Dieses Verfahren wurde ursprünglich verwendet, um vollfarbige Prototypen und Modelle aus Sandstein herzustellen. Eine Variante des Verfahrens erfreut sich aufgrund seiner Möglichkeiten zur Chargenproduktion derzeit wachsender Beliebtheit.
Der Druckschritt beim Metall Binder Jetting erfolgt bei Raumtemperatur. Dies bedeutet, dass thermische Effekte (wie Verwerfungen und innere Spannungen) wie bei DMLS/SLM kein Problem darstellen und keine Abstützung erforderlich ist. Ein zusätzlicher Nachbearbeitungsschritt ist erforderlich, um ein Vollmetallteil zu erstellen.
Wie funktioniert Metall Binder Jetting?
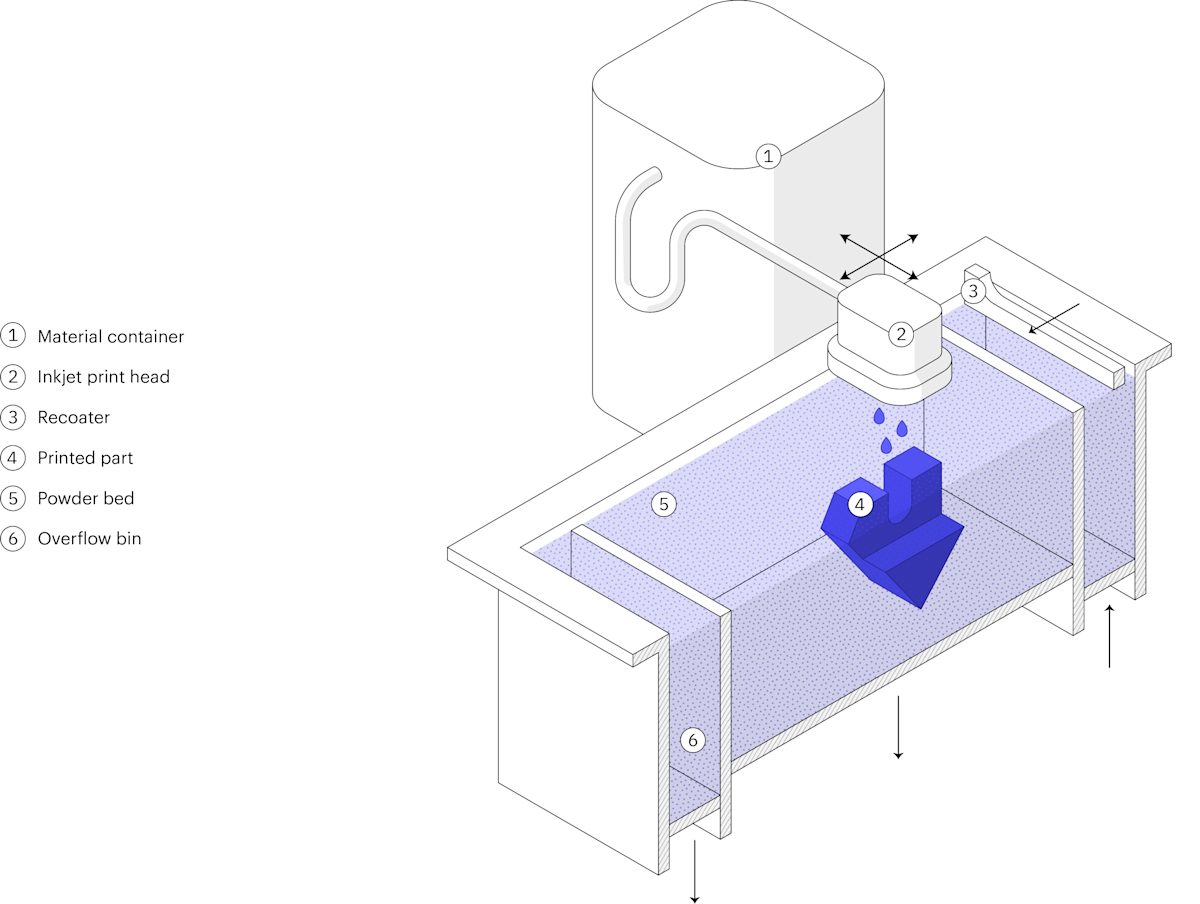
Metall Binder Jetting ist ein zweistufiger Prozess. Er beinhaltet einen Druckschritt und einen wesentlichen Nachbearbeitungsschritt. Und so funktioniert der Druckprozess:
- Eine dünne Schicht Metallpulver (typisch 50 μm) wird auf der Rohlingplattform verteilt.
- Ein Wagen mit Tintenstrahldüsen fährt über das Bett und scheidet selektiv Tröpfchen eines Bindemittels (Polymer und Wachs) ab, die die Metallpulverteilchen verbinden.
- Wenn eine Schicht fertig ist, fährt die Rohlingplattform herunter und der Vorgang wird wiederholt, bis das gesamte Werkstück fertiggestellt ist.
Das Ergebnis des Druckvorgangs ist ein Teil im sogenannten „rohen“ Zustand. Es ist ein Nachbearbeitungsschritt erforderlich, um das Bindemittel zu entfernen und vollständig metallische Teile herzustellen.
Für diesen Nachbearbeitungsschritt gibt es zwei Varianten:
- Durchdringung: Vom Rohling wird zuerst das Bindemittel abgewaschen, um ein „braunes“ Teil mit starker innerer Porosität (~ 70%) zu erzeugen. Das „braune“ Teil wird dann in einem Industrieofen in Gegenwart eines Metalls mit niedrigem Schmelzpunkt (typischerweise Bronze) erhitzt. Die inneren Hohlräume werden aufgefüllt, was zu einem „Bimetallteil“ führt.
- Sintern: Der Rohling wird in einen Industrieofen gegeben. Dort wird zunächst das Bindemittel abgebrannt und anschließend die restlichen Metallpartikel miteinander versintert. Das Ergebnis ist ein Vollmetallteil mit Abmessungen, die etwa 20% kleiner sind als das ursprüngliche „rohe“ Teil. Um diese Schrumpfung auszugleichen, werden die Teile größer gedruckt.
Heutzutage wird in den meisten Anwendungen das Sintern eingesetzt, da durch die Durchdringung Teile mit schlechteren Materialeigenschaften und einem nicht gut dokumentierten mechanischen und thermischen Verhalten entstehen.
Binder Jetting und Metallspritzguss (MIM)
Binderauftragteile haben nach dem Sintern sehr ähnliche Eigenschaften wie Teile, die mit MIM hergestellt wurden. MIM ist ein Herstellungsverfahren, mit dem fast jedes kleine Metallteil, das heutzutage in der Unterhaltungselektronik oder im Auto vorkommt, in Serie hergestellt wird.
MIM ist eine Variante des Kunststoffspritzgussverfahrens. In ein Kunststoffbindemittel eingemischtes Metallpulver wird in eine Form eingespritzt, um den Rohling zu erhalten, der dann gesintert wird, um zu Metall zu werden.
Metallbinder-Auftrag baut also auf dem Know-how des MIM-Prozesses auf.
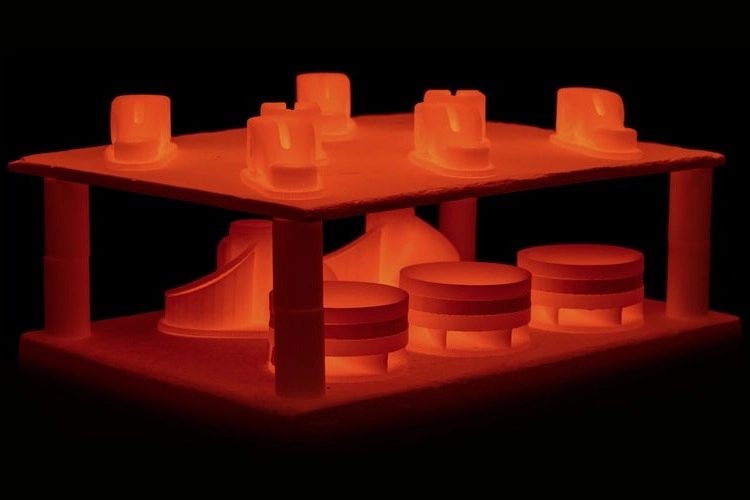
Vorteile und Einschränkungen des Metall Binder Jettings
Binder Jetting ist heute die einzige 3D-Metalldrucktechnologie, die kostengünstig für die Produktion von Metallteilen in kleinen bis mittleren Stückzahlen eingesetzt werden kann.
Da zum Drucken keine Stützstrukturen benötigt werden, können Binder Jetting-Systeme ihr gesamtes Bauvolumen nutzen. Dies ermöglicht es, selbst bei kleinen bis mittleren Stückzahlen kostengünstig mit der herkömmlichen Fertigung zu konkurrieren.
Darüber hinaus weisen Teile, die per Binder Jetting hergestellt werden, eine glattere Oberfläche und schärfere Kanten als DMLS/SLM-Teile auf, sodass zusätzliche Endbearbeitungsvorgänge möglicherweise entfallen können. Im Vergleich zu DMLS/SLM sind auch die Kosten für das Rohmetallpulver niedriger, was eine große Rolle für den Stückpreis spielt.
Andererseits haben mit Binder Jetting hergestellte Teile immer eine innere Porosität von etwa 0,2 bis 2%. Beachten Sie, dass innere Hohlräume die in den technischen Datenblättern angegebene Zugfestigkeit möglicherweise nicht beeinträchtigen, jedoch die Ermüdungsfestigkeit eines Teils erheblich verringern können.
Denken Sie daran, dass der Sinterschritt mit einer erheblichen Schrumpfung der Teile verbunden ist. Diese Schrumpfung ist inhomogen und schwer mit hoher Präzision vorherzusagen. In der Praxis werden mehrere Probedrucke benötigt, um eine CAD-Datei zu erhalten, die das Teil mit den gewünschten Endabmessungen erzeugt. Die Wiederholbarkeit des Prozesses ist jedoch hervorragend. Dies bedeutet, dass nach erfolgreicher Kalibrierung größere Mengen dieses Teils hergestellt werden können.
Technische Eigenschaften des Metall Binder Jettings
In der folgenden Tabelle sind die grundlegenden technischen Funktionen eines typischen 3D-Druckers mit Metall Binder Jetting zusammengefasst. Weitere Gestaltungsrichtlinien finden Sie unter Gestaltungsregeln.
Eigenschaft | Metall Binder Jetting |
---|---|
Materialauswahl | Derzeit begrenzt Edelstahl, Werkzeugstahl, Hartmetall |
Maßhaltigkeit | ± 0,2 mm (± 0,1 nach Versuchen) |
Typische Werkstückgröße | 400 x 250 x 250 mm (-20% effektive Werkstückgröße nach dem Sintern) |
Übliche Schichtdicke | 35 - 50 μm |
Typische Oberflächenrauheit | RA 6 μm |
Abstützung | Nicht zum Drucken erforderlich |
Innere Porosität | Zwischen 0,2 und 2,0% |
Kosten pro Teil | $$$ |
Part 4
Metallextrusion
Metallextrusion ist ein alternatives, kostengünstiges 3D-Metalldruckverfahren, das sich hauptsächlich für Prototyping-Zwecke oder für einmalige kundenspezifische Teile eignet.
In diesem Abschnitt werden die Merkmale und Hauptvorteile und -einschränkungen dieses additiven Verfahrens eingehend untersucht, damit Sie besser verstehen, wie es am effektivsten eingesetzt wird.
Was ist 3D-Druck per Metallextrusion?
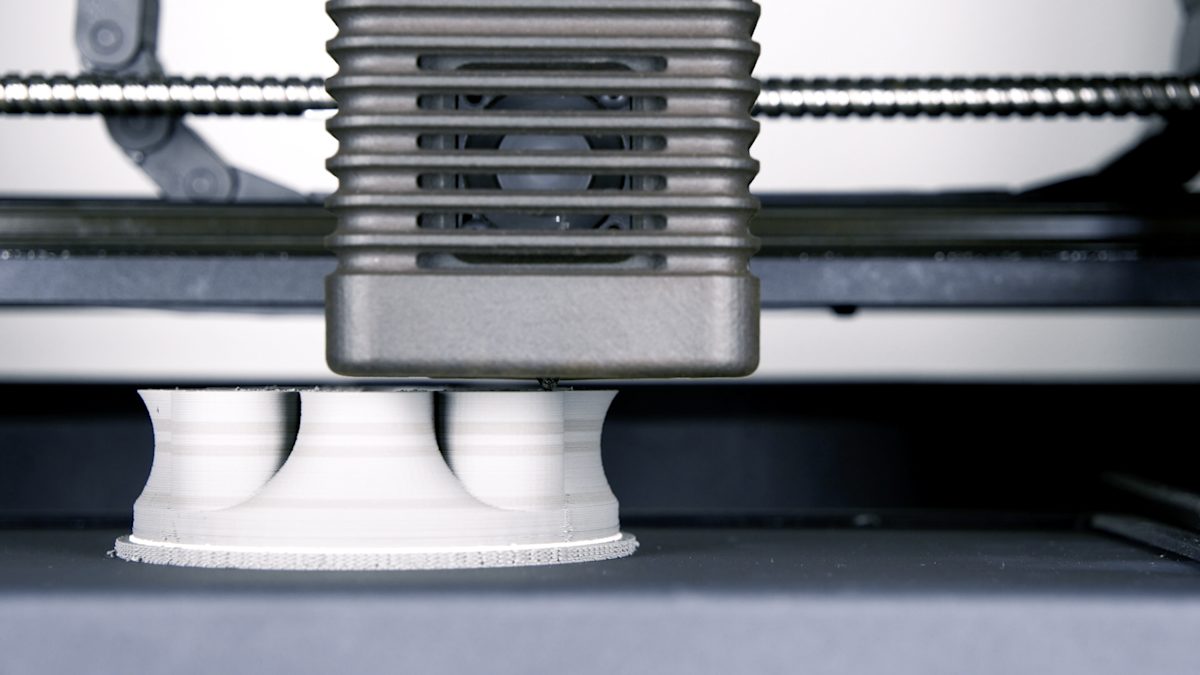
Metallextrusion ist eine Variante des klassischen FDM-Verfahrens für Kunststoffe. Die ersten 3D-Drucker für die Metallextrusion wurden 2018 auf den Markt gebracht. Die Technologie ist auch unter den Namen Bound Metal Deposition (BMD) oder Atomic Diffusion Additive Manufacturing (ADAM) bekannt.
Wie bei FDM wird ein Teil Schicht für Schicht aufgebaut, indem Material durch eine Düse extrudiert wird. Im Gegensatz zu FDM ist das Material kein Kunststoff, sondern ein Metallpulver, das mit einem Polymerbindemittel zusammengehalten wird. Das Ergebnis des Druckschritts ist ein „rohes“ Teil, das vom Binder befreit und gesintert werden muss, um vollständig aus Metall zu werden.
Wie funktioniert die Metallextrusion?
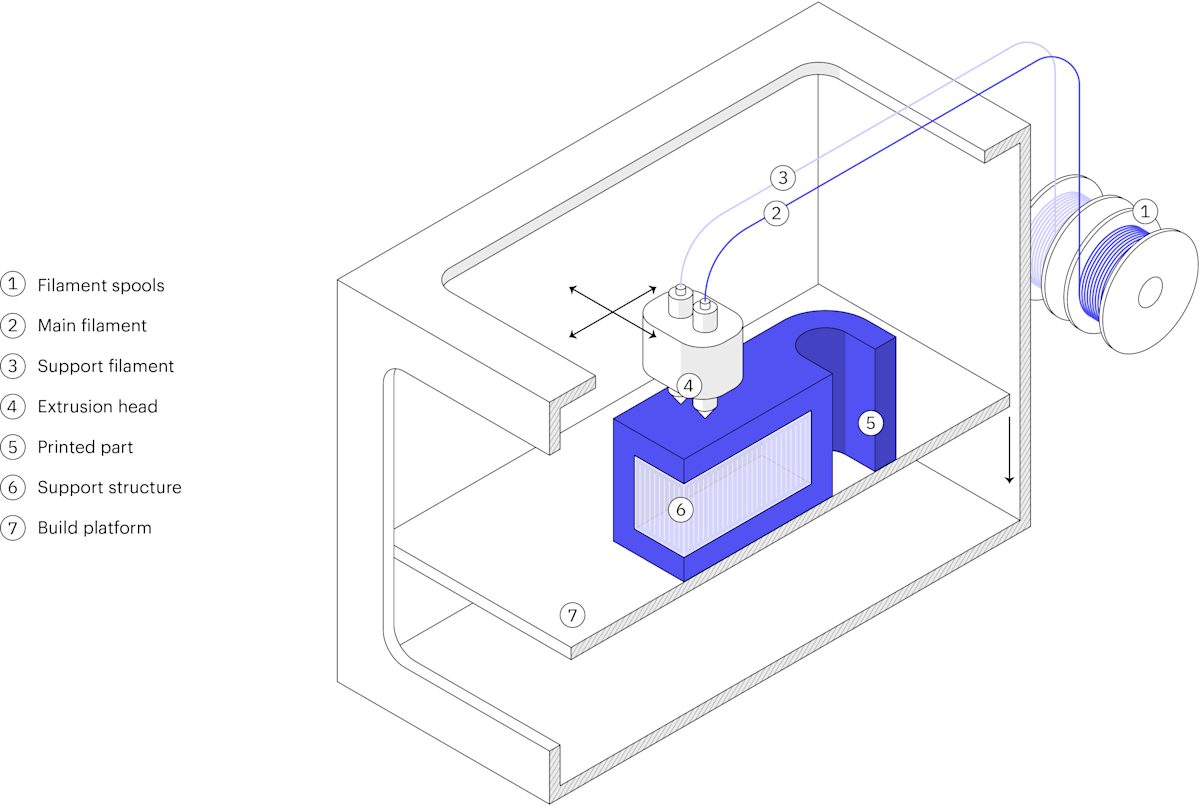
Die Metallextrusion ist ein dreistufiger Prozess. Sie umfasst einen Druckschritt, einen Binderentfernungsschritt und einen Sinterschritt. So funktioniert der Druckschritt:
- Das Rohmaterial liegt in Form eines Filaments oder einer Stange vor, die typischerweise aus Metallpartikeln besteht, die durch Polymer und/oder Wachs miteinander verbunden sind.
- Dieser Stab oder Faden wird durch eine beheizte Düse extrudiert und schichtweise aufgetragen, wobei ein Teil auf der Grundlage des CAD-Modells aufgebaut wird.
- Gleichzeitig werden bei Bedarf Stützstrukturen aufgebaut. Die Schnittstelle zwischen dem Träger und dem Teil ist mit einem keramischen Trägermaterial bedruckt, das später leicht manuell entfernt werden kann.
Wenn der Druck abgeschlossen ist, muss das resultierende „rohe“ Teil nachbearbeitet werden, um mit ähnlichen Schritten wie beim Binder Jetting zu Metall zu werden. Der Rohling wird zuerst mehrere Stunden in einer Lösung gewaschen, um den größten Teil des Bindemittels zu entfernen. Anschließend wird er in einem Ofen gesintert, um die Metallpartikel miteinander zu verbinden und ein Vollmetallteil zu bilden.
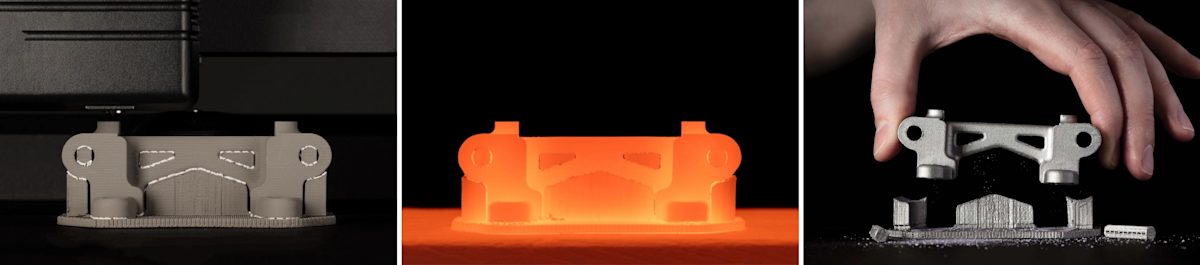
Beim Sintern reduzieren sich die Teileabmessungen um ca. 20%. Um dies auszugleichen, werden die Teile entsprechend größer gedruckt. Wie beim Binderauftrag ist diese Schrumpfung nicht homogen. Dies bedeutet, dass einige Versuche und Irrtümer erforderlich sind, um genaue Ergebnisse für ein bestimmtes Design zu erzielen.
Metallextrusion FDM aus Kunststoffen
Die Art und Weise, wie die Drucker für Metallextrusion und Plastik-FDM funktionieren, ist sehr ähnlich. Beispielsweise drucken beide Prozesse Teile hohl, wobei ein Zellenumriss und eine Füllung verwendet werden.
Neben dem Material gibt es zwei weitere wichtige praktische Unterschiede zwischen Metallextrusion und FDM, die Sie berücksichtigen sollten. Beide sind mit der Mechanik des Binderentfernungs- und Sinterprozesses verbunden.
- Wandstärke: Bei der Metallextrusion sollten Teile immer eine gleichbleibende Wandstärke haben (vorzugsweise kleiner als 10 mm). Ist dies nicht der Fall, kann sich die Zeit zur vollständigen Binderentfernung und zum Sintern der Teile um mehrere Stunden erhöhen.
- Abstützungsstrukturen: Wie bei FDM sind bei der Metallextrusion Stützelemente während des Drucks häufig erforderlich. Bei der Metallextrusion ist jedoch auch eine Abstützung beim Sinterschritt erforderlich. Bei diesen sehr hohen Temperaturen wird das Metallmaterial weich und biegsam und kann unter seinem eigenen Gewicht zusammenbrechen.
Vorteile und Einschränkungen der Metallextrusion
Die Metallextrusion eignet sich hervorragend für funktionale Prototypen und kleine Produktionsserien von Metallteilen, für deren Herstellung ansonsten eine 5-Achsen-CNC-Bearbeitung erforderlich wäre.
Mit einem Bruchteil der Kosten von DMLS/SLM oder Binder Jetting sind Metallextrusionsdrucker das wirtschaftlichste Metalldrucksystem, das es bisher gibt. Auf diese Weise kann ein breiteres Publikum von den Hauptvorteilen des 3D-Metalldrucks (optimierte Strukturen, Bauteilezusammenführung, interne Kanäle) profitieren, insbesondere für den Prototypenbau und Kleinserien. Darüber hinaus sind diese Systeme aufgrund ihrer Benutzerfreundlichkeit und ihrer geringen Anforderungen an Gesundheit und Sicherheit für die Eigenfertigung von kundenspezifischen Teilen oder Werkzeugen zur Unterstützung anderer Vorgänge geeignet.
Im Vergleich zu anderen Fertigungstechnologien (wie CNC-Bearbeitung und Blechbearbeitung) sind die Kosten für die Metallextrusion jedoch immer noch beträchtlich. Bei einfachen Geometrien ist es wirtschaftlicher (und in der Regel schneller), ein traditionelles Herstellungsverfahren zu wählen, selbst wenn die Produktion ausgelagert wird. Der größte Beitrag zu diesen endgültigen Kosten ist die Zeit, die erforderlich ist, um die gedruckten „rohen“ Teile von Binder zu befreien und zu sintern. Dies dauert im Durchschnitt 24 bis 72 Stunden.
Aus technischer Sicht sind die mit diesen Systemen hergestellten Teile nicht für anspruchsvolle Anwendungen geeignet, da sie aufgrund ihrer inneren Porosität (ca. 2-4%) schlechtere mechanische Eigenschaften aufweisen als Schmiedemetall (~ 33% geringere Festigkeit).
Technische Eigenschaften der Metallextrusion
In der folgenden Tabelle sind die grundlegenden technischen Funktionen eines typischen 3D-Druckers für Metallextrusion zusammengefasst. Weitere Gestaltungsrichtlinien finden Sie in den Konstruktionsregeln.
Eigenschaft | Metallextrusion |
---|---|
Materialauswahl | Derzeit sehr begrenzt Edelstahl |
Maßhaltigkeit | ± 0,5 mm mit einer Untergrenze von ± 0,5 mm |
Typische Werkstückgröße | 300 x 200 x 200 mm (-20% effektive Werkstückgröße nach dem Sintern) |
Übliche Schichtdicke | 50 - 200 μm |
Abstützung | Erforderlich zum Drucken und Sintern |
Innere Porosität | Zwischen 2,0 und 4,0% |
Kosten pro Teil | $$$ |
Part 5
Design für den 3D-Metalldruck
Das Entwerfen für den 3D-Metalldruck erfordert eine neue Denkweise und verfügt über einzigartige Designregeln und eigene gute Praktiken.
In diesem Abschnitt stellen wir Ihnen die grundlegenden Prinzipien und Tools vor, mit denen Sie Ihre Entwürfe optimal nutzen können, z. B. die Topologieoptimierung.
Zu berücksichtigende Designaspekte
Das Design für einen additiven Prozess folgt anderen Regeln als das Design für die „traditionelle“ Fertigung. Die einzigartige Gestaltungsfreiheit sowie die einzigartigen Beschränkungen erfordern ein Umdenken des Designers.
Hier ist eine Liste der wichtigsten Ideen, die Sie beim Design für den 3D-Metalldruck berücksichtigen sollten:
Wichtige Design-Überlegungen
Aufgrund der hohen Kosten ist es selten wirtschaftlich möglich, Teile mit 3D-Metalldruck herzustellen, die für ein traditionelles Verfahren entwickelt wurden.
Tatsächlich ist es technisch oft unmöglich, diese Geometrien zu reproduzieren. Beispielsweise neigen Querschnitte mit einer Dicke von mehr als 10 mm dazu, sich zu verziehen oder zu anderen Herstellungsfehlern und sollten vermieden werden.
Designkomplexität wird oft als schädlich betrachtet, weil sie mit erhöhten Kosten verbunden sei. Beim 3D-Metalldruck ist dies nicht der Fall. Im Gegenteil, um die Vorteile des 3D-Metalldrucks voll auszuschöpfen, ist es entscheidend, einen Weg zu finden, den Mehrwert zu maximieren, den geometrische Komplexität für ein System mit sich bringt.
Wenn Sie ein Teil oder eine Baugruppe für den 3D-Metalldruck neu entwerfen, ist es normalerweise sinnvoll, mit einer ganz leeren Arbeitsfläche zu beginnen. Auf diese Weise können Sie vermeiden, durch vorgefasste Designs eingeschränkt zu werden.
Entscheidend ist dabei die eindeutige Definition der Designanforderungen (Lasten, Randbedingungen, Teilegewicht etc.). Wir werden im nächsten Abschnitt sehen, dass moderne CAD-Software diese als Eingabe verwendet, um optimierte Strukturen mit organischen Formen zu erstellen.
Es ist eine gute Praxis, eine klare Vorstellung davon zu haben, wie das Teil in der Maschine ausgerichtet sein wird. Die Druckausrichtung ist wichtig, da sie die Position und den Bedarf von Stützstrukturen festlegt.
Das Ziel des Konstrukteurs sollte es sein, Teile mit selbsttragenden Merkmalen zu erstellen, um den Bedarf an Abstützung zu minimieren und den Erfolg des Aufbauens sicherzustellen.
Unabhängig vom Prozess ist im 3D-Metalldruck immer eine Nachbearbeitung erforderlich. Dies kann obligatorisch sein (wie das Entfernen von Abstützelementen beim DMLS/SLM oder das Sintern beim Binder Jetting und der Metallextrusion) oder optional (wie ein CNC-Bearbeitungsschritt, um engere Toleranzen zu erzielen, oder eine Wärmebehandlung, um die Materialeigenschaften zu verbessern).
Daher ist es wichtig, die Nachbearbeitungsanforderungen und die verfügbaren Optionen im Kopf zu behalten, während Sie ein Teil für den 3D-Metalldruck entwerfen.
Tools und Software zur Designoptimierung
Moderne CAD-Pakete bieten Tools, mit denen Sie die geometrische Freiheit des 3D-Metalldrucks voll ausschöpfen können. Mit diesen algorithmischen Entwurfswerkzeugen können Sie organische Strukturen erstellen, die Teile übertreffen, die mit herkömmlichen Methoden entworfen wurden.
Es gibt drei Hauptstrategien, die heute angewendet werden können. Diese Strategien können entweder die Leistung eines vorhandenen Entwurfs optimieren oder bei der Erstellung von Strukturen von Grund auf, nämlich auf der Grundlage einer Reihe von Entwurfsanforderungen helfen.
Gitterstrukturen
Das Anwenden eines Gittermusters ist eine hervorragende Möglichkeit, ein vorhandenes Design zu optimieren.
Gitterstrukturen können leichte Teile erzeugen, die Oberfläche von Wärmetauschern maximieren oder die Bedruckbarkeit verbessern und die Herstellungskosten eines vorhandenen Designs senken.
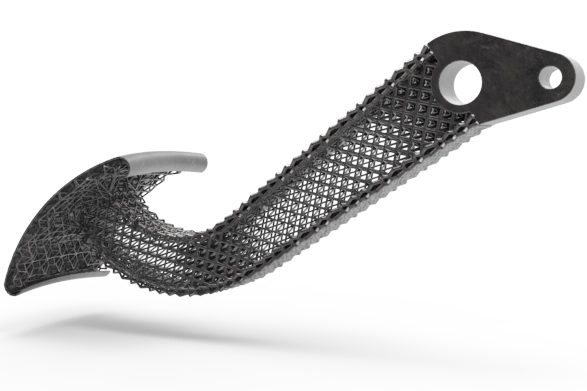
Topologieoptimierung
Die simulationsgesteuerte Topologieoptimierung hilft bei der Erstellung von Strukturen mit minimaler Masse und maximaler Steifigkeit.
Bei der Topologieoptimierung werden der benutzerdefinierte Entwurfsraum und die Lastfälle analysiert, um die Bereiche zu bestimmen, aus denen Material entfernt werden kann. Das Ergebnis der Simulation kann dann verwendet werden, um Teile für optimale Leistung in diesen Belastungsszenarien zu entwerfen.
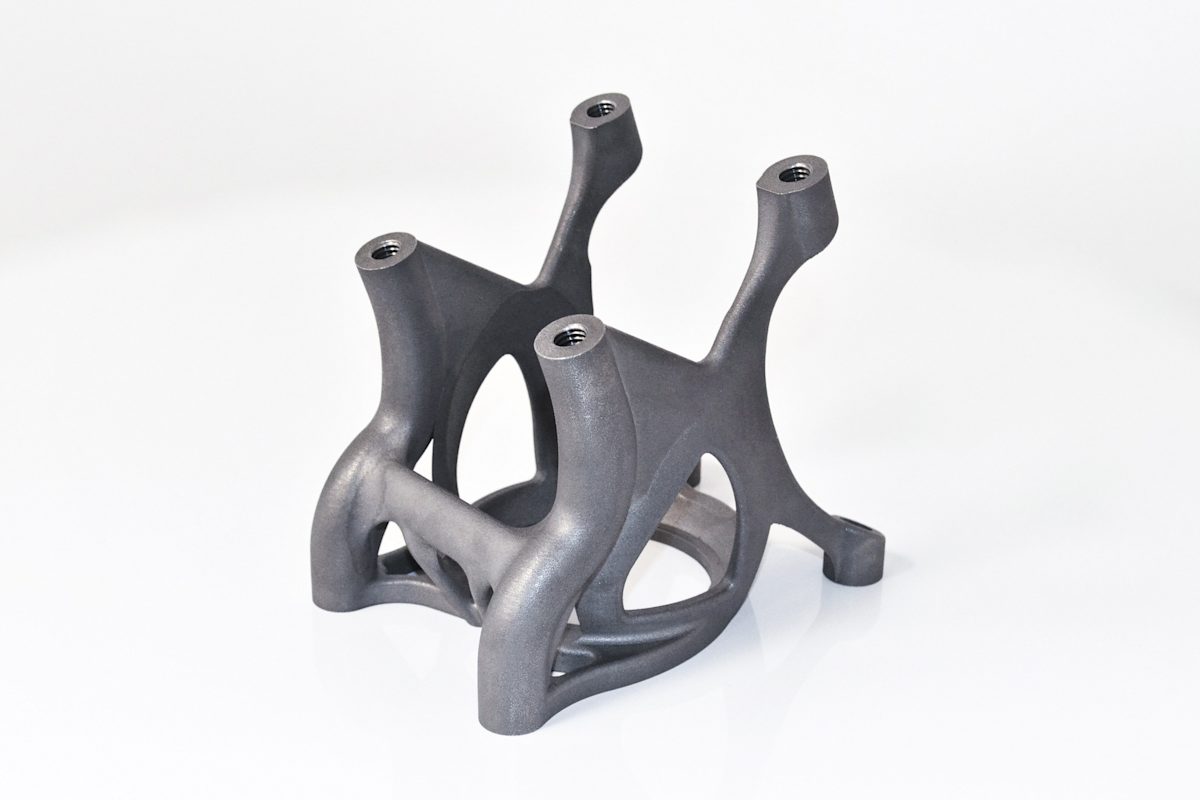
Generatives Design
Generatives Design ist eine Variation des simulationsgesteuerten Topologieoptimierungsprozesses.
Beim generativen Design werden bei der Analyse anstelle einer einzelnen Ausgabe mehrere Designkandidaten erstellt. Die resultierenden Designs sind alle herstellbar und erfüllen die Designanforderungen. Auf diese Weise kann der Designer verschiedene Lösungen untersuchen und diejenige auswählen, die zur Anwendung passt (z. B. basierend auf sekundären Kompromissen).
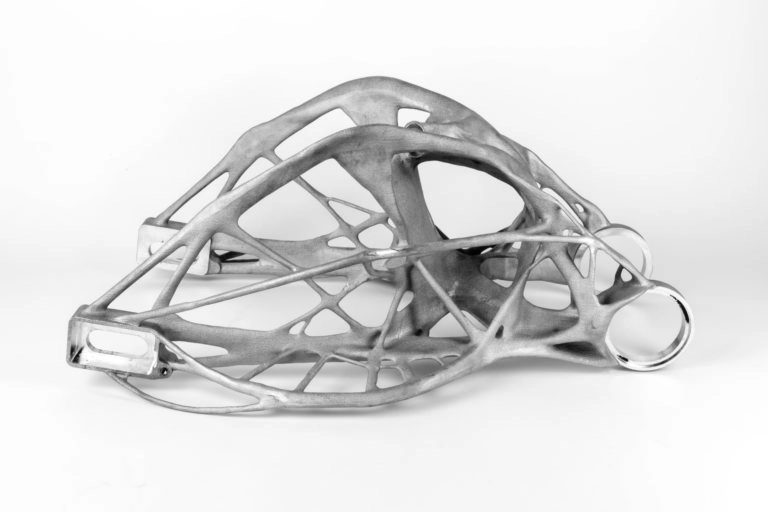
Es wird dringend empfohlen, eine dieser fortschrittlichen CAD-Techniken zu verwenden - insbesondere beim Entwerfen von DMLS/SLM-Teilen. Nachfolgend haben wir eine kurze Liste von CAD-Paketen zusammengestellt, die Tools zur Konstruktionsoptimierung für den 3D-Metalldruck bieten, um Ihnen den Einstieg zu erleichtern:
Designregeln
Selbst wenn Sie moderne CAD-Tools verwenden, müssen Sie bestimmte Konstruktionsrichtlinien befolgen. Diese haben mit der Grundmechanik der 3D-Metalldruckprozesse zu tun. Hier eine Liste der wichtigsten Gestaltungsregeln:
Minimale Wandstärke
DMLS / SLM: 0,4 mm
Binderauftrag per Düse: 1,0 mm
Metallextrusion: 1,0 mm
Binder Jetting- und Metallextrusions-Teile sind im „rohen“ Zustand zerbrechlich. Dickere Wandquerschnitte verringern die Wahrscheinlichkeit eines Bruchs.

Maximales Seitenverhältnis
DMLS/SLM: 8: 1
Binderauftrag: 8: 1
Metallextrusion: 8: 1
Über Stützrippen (ähnlich wie beim Spritzgießen) können hohe Werkstückdetails besonders stabilisiert werden.

Kleinste Strukturgröße
DMLS/SLM: 0,6 mm
Binderauftrag: 2,0 mm
Metallextrusion: 3,0 mm
Isolierte Merkmale sind beim Drucken oder bei der Handhabung anfälliger als Wandabschnitte. Verwenden Sie für Stifte lieber einen handelsüblichen Einsatz.

Minimale Detailgröße
DMLS / SLM: 0,4 mm
Binder Jetting: 0,1 mm
Metallextrusion 0,5 mm
Die maximale Detailauflösung hängt von der Größe des Lasers, des Bindertropfens oder der Düse ab.

Minimaler Lochdurchmesser
DMLS/SLM: Ø1,5 mm
Binderauftrag: Ø 1,0 mm
Metallextrusion: Ø1,5 mm
Verwenden Sie bei Löchern, die nicht entlang der Rohlingrichtung ausgerichtet sind, besser eine Tropfenform, um die Notwendigkeit einer Abstützung zu vermeiden.
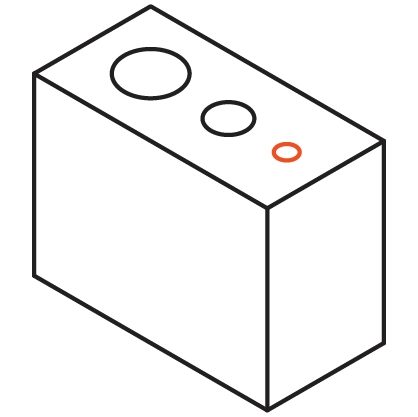
Maximaler Überhangwinkel
DMLS / SLM: 50°
Binderauftrag: nicht zutreffend
Metallextrusion: 45°
Möglicherweise ist eine zusätzliche Abstützung für das Sintern beim Binder Jetting und bei der Metallextrusion erforderlich.

Nicht abgestützte Kanten
DMLS / SLM: 0,5 mm
Binderauftrag: 20 mm
Metallextrusion 0,5 mm
Erwägen Sie, den Überhang zu beseitigen, indem Sie eine 45° -Fase unter den nicht abgestützten Kanten hinzufügen.
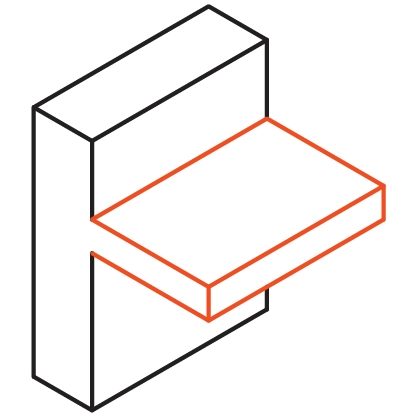
Folgen Sie den Links unten, um mehr über die Konstruktion für die verschiedenen 3D-Metalldruckverfahren zu erfahren:
Part 6
Hilfreiche Ressourcen
In diesem Handbuch haben wir alles angesprochen, was Sie für den Einstieg in den 3D-Metalldruck benötigen. Es gibt jedoch noch viel mehr zu lernen.
Im Folgenden finden Sie die besten und nützlichsten Ressourcen zum 3D-Metalldruck und anderen digitalen Fertigungstechnologien für diejenigen, die sich eingehender mit diesem Thema befassen möchten.
Protolabs Network Wissensbasis
Hier haben wir alles angesprochen, was Sie für den Einstieg in den 3D-Druck benötigen. In unserer Wissensbasis, einer Sammlung technischer Artikel zu allen Fertigungstechnologien, die von Experten von Protolabs Network und der Fertigungsindustrie verfasst wurden, gibt es noch viel mehr zu erfahren.
Hier finden Sie eine Auswahl unserer beliebtesten Artikel zum Thema 3D-Druck:
Leitfäden zu anderen Fertigungstechnologien
Möchten Sie mehr über Digitale Fertigung erfahren? Es gibt noch mehr Technologien zu erforschen:
Benötigen Sie 3D-gedruckte Metallteile?
Zu Protolabs.com