
Online injection molding service
Access a wide range of custom services from our specialized network of injection molding companies. Prototype and production tooling. Upload your parts for a free quote and expert feedback.
Get an injection molding quote All uploads are secure and confidentialOur custom injection molding services
Create parts of all complexities sized from 3 mm (0.12 in) to 2 m (79 in) with Protolabs Network. Lead times are as fast as 10 days, and we offer local or global production options. Our manufacturing partners typically use 20 to 3,000 ton injection machines, depending on part size, complexity, and volume. DIN 16901-130 and tighter tolerances are available on request.

Injection molding is the manufacturing process of injecting high-pressure thermoplastic into a mold. Ideal for high-volume production.

A manufacturing process in which a part is molded around a pre-installed insert in the tooling.

A manufacturing process in which one plastic material is molded over another to create a single component.

A thermoset process that involves mixing a two-part solution together to produce flexible and durable parts.
Tooling - prototyping vs production

Ideal for rapid prototyping and low-volume production
-
Tool shot life – 1k to 100k units
-
Fast turnaround and cost-efficient construction
-
Aluminum or steel

Longer-lasting tooling for larger volumes
-
Tool shot life – 100k to 1M units
-
Automated production for cost-efficiency at higher volumes
-
Hardened steel for longer life and a scalable unit price
Secondary operations
We offer several secondary operations such as painting or heat tapping inserts. You can specify which secondary operations are needed in the “custom requirements” part of your quote request. Here are some examples of secondary operations we provide:










Gallery of plastic injection molded products



Injection molding surface finishes

We offer any type of SPI surface finish, such as A-1, D-2 or D-3.

We offer any type of VDI surface finish, such as VDI28, VDI30 or VDI 33.
Injection molding materials
Injection molding uses a huge range of plastics, making it ideal for many applications across nearly every industry. We can source thousands of materials on request. Please contact networksales@protolabs.com for specific material requests.
Explore our IM materials
Property | Materials |
---|---|
Impact resistant | ABS, PMMA, PVC, PE, PC |
Wear-resistant | POM, PEEK, UHMW |
Dimensional stability | ABS, PBT, HIPS, PPS |
Chemical resistance | PEEK, PP, PBT, PE, LDPE, PA |
Rubber like | TPU, TPE, Silicone |
Cost-efficient | PP, HDPE, LDPE |
Cosmetic | ABS, PC, HIPS |
How we manage your injection molding project
Upload your parts to our platform to have your project reviewed by our team
Your account manager will work with our technical team and manufacturing partners to send you a quote within 48 hours
Receive extensive Design For Manufacturing analysis to approve before construction of your tool begins
We send you a golden sample for approval before starting production
We produce your parts to match the golden sample & deliver them to you
You can easily reorder parts by contacting your account manager
The injection molding timeline
Ready to start the injection molding process? Download our Gantt chart to help keep your injection molding project on schedule, within budget and to spec.

The Protolabs Network Standard - consistent quality, every time
Protolabs Network applies a rigorous set of standards to every custom part, ensuring quality and consistency for injection molded components. We inspect each order dimensionally and visually during and after production.
Our injection molding team
Manufacturing doesn’t have to be an anonymous process. We have a dedicated team of injection molding project engineers and support staff on the ground to help make sure everything runs smoothly and on time, every time.

"I take care of your parts from start to finish, making sure you receive the parts on time and exactly as you requested.”

“I guarantee that your parts go through an extensive quality control process, so they will always be up to spec.”

“I make sure we always have a manufacturing partner in our network that fits your manufacturing needs.”

“I ensure our customers are constantly updated on the status of the project and guarantee that they experience a smooth ordering process.”
Enabling companies to injection mold for the future
Learn how LEKTRI.CO designed its new chargers and how we built the robust casing and cover to match its futuristic design.
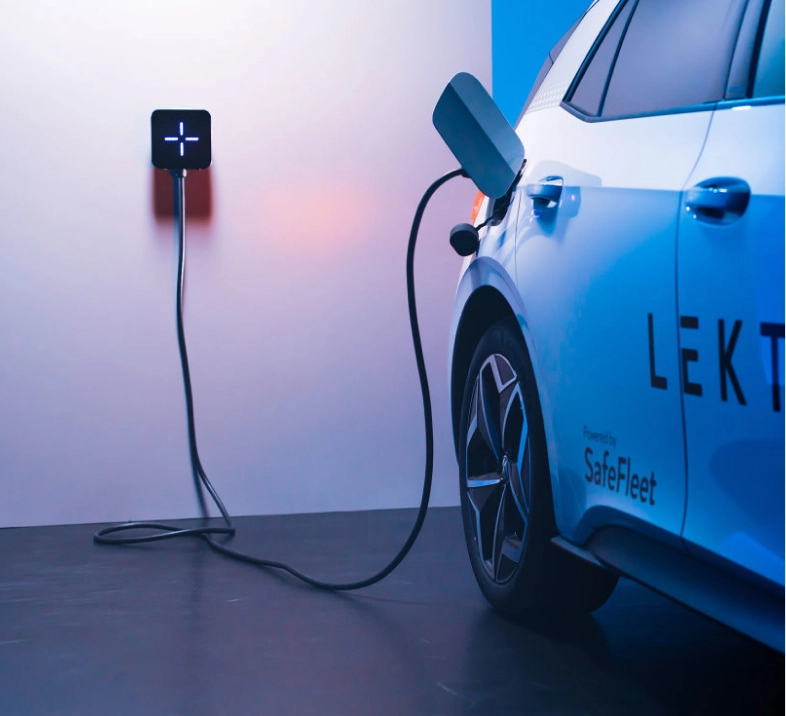
More resources for injection molding
Learn more about how injection molding works and how to design the best parts for this technology.
Want to learn more about injection molding? |
---|
- Injection molding guide
- What are the common applications of injection molding and its top benefits?
- How to avoid common defects in injection molding
- What’s the best SPI surface finish for your injection molded part?
- How do you design parts for injection molding?
- What is injection molding?
- Why is draft angle design essential for injection molding?
FAQ’s
How much does plastic injection molding cost?
There are many factors that determine the cost of injection molding your custom parts. The three main expenses are tooling, materials and production. Find out how to reduce your manufacturing costs in our injection molding guide.
Who owns the injection mold?
Customers retain ownership of all custom tooling they develop, however, any reusable proprietary components developed by the manufacturing partner (MP) will become the MP’s property. All custom tooling will remain at the MP’s facility for a minimum of two years unless otherwise agreed. If the tooling is inactive after two years, the MP may contact Protolabs Network to determine if the tool must be retained for additional time. Protolabs Network will then contact the customer to make further arrangements. Molds can be transferred to any desired location upon request and at the requester's expense.
What happens if an injection molding partner leaves our network?
Whenever a manufacturing partner leaves our network, we carry the cost of transferring all molds to another MP in the network, ensuring that your parts get delivered on time.
What is the available capacity/timeline for reorders?
In general, we have the RFQ ready within 24 hours. It takes two days to set up the mold and order and process the materials, and one day for packing and sending the order out to be shipped. The volume of your parts will determine the number of days required for manufacturing.
What ISO certifications do you have?
We work with a network of specialized injection molding companies that have ISO 9001 and ISO/TS16949 certifications.
How long do you store my mold for?
Your injection molding mold is kept at our manufacturing partner facilities for reuse for a minimum of 2 years.
If you would like to reorder from your mold, please contact your account manager or networksales@protolabs.com.
Our other manufacturing capabilities

Milling (3-, 4- & full 5-axis), turning and post-processing
-
50+ metals and plastics & 10 surface finishes
-
Tolerances down to ±.0008 in (0.020 mm)
-
Lead times from 5 business days

FDM, SLA, SLS, MJF
-
25+ plastics & 35+ colors
-
±0.5% dimensional accuracy with a lower limit down to ±0.0059 in (0.15 mm)
-
Lead times from 1 business day

Laser cutting, bending, post-processing
-
6 metals & 9 surface finishes
-
Tolerances down to ±.004 in (0.010 mm)
-
Lead times from 5 business days
Put your injection molded parts into production
Get an injection molding quote